|
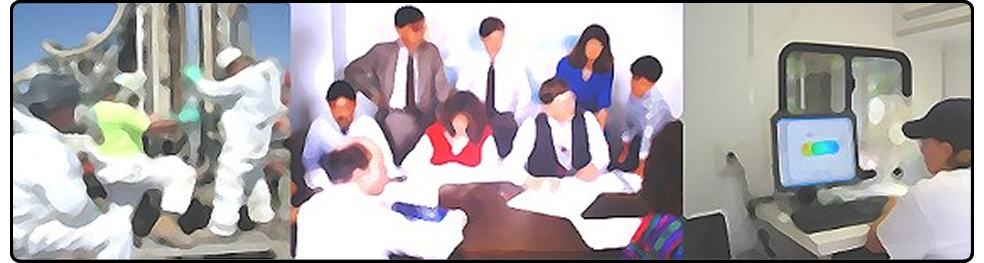
GeoSierra's PRB Design/Build and Inclusion Propagation Technologies
|
The genesis of GeoSierra's patents, specialized
equipment, and expertise for its "trenchless construction" of deep
PRBs was the discovery in 1992 that it was possible to induce and control the
direction (orientation pathway) of a vertical fracture in certain soils. From
this discovery the idea was conceived to perfect the process of controlled
vertical hydraulic fracturing with the objective of then being able to apply
the process as a key technology component for installation of PRB walls in the
subsurface. An extensive series of hydraulic fracturing experiments in soils
and weakly cemented sediments was then completed by conducting over 250 tests
in a variety of soil conditions. These tests and experiments were excavated to
verify the extent, orientation and thickness of the resulting vertical
hydraulic fractures.
These experiments proved the eariler discovery that by
creating an artificial fracture at the required azimuth in the soil, controlled
vertical hydraulic fracturing of the soil could be maintained and fracture
coalescence between multiple injections could be assured, thus providing the
subsurface pathway for the formation of an iron PRB wall. It was the discovery
in 1992 that ultimately led to the four patents being awarded to GeoSierra from
1999 through 2002 with respect to its proprietary technologies design, real-time imaging and for
installation of iron PRBs.
Since then the technology has been further developed
for enhanced oil and gas recovery leading to some twenty patents being awarded
in Argentina, AGS, Bolivia, China, Canada, Columbia, Ecuador, Indonesia,
Mexico, Russia and Federated States, and the USA. The comparison of offset
conventional wells and split casing stimulated wells in the Milk River tight
gas reservoir demonstrated the science behind inclusion propagation in ductile
formations at depth. |
|
1993 First Generation of Fracture Initiation Device Demonstrated |
|
One of the forerunners of GeoSierra's fracture technology was field demonstrated in 1993 as a proof of concept under contract to the U.S. Army Corps of Engineers at a site in New Hampshire. These demonstration tests utilized the earliest form of the fracture initiation device consisting of a driven flat-faced probe with an inflatable packer mounted above the probe. The proof of concept demonstrated, from the initiation and propagation of twenty-three vertical hydraulic fractures, that fracture azimuth could be controlled and maintained, fracture coalescence of multiple injected fractures could be assured, and fracture thickness of up to 9" could be accomplished. |
1997 Second Generation and First Commercial Fracture Initiation Device Employed |
|
The first commercial fracture initiation device developed by GeoSierra was a twelve (12) ft long tool, 6" in diameter, that was inserted into a 6.25" diameter PVC casing pre-drilled and grouted into the soil to the full depth of the required fracture. The tool was a chain saw cutting device that, upon insertion to the required depth, cut the PVC casing and grout and could then create a 5 ft long vertical cut in the soil extending upwards to 20 ft high. This fracture initiation device was developed for two (2) markets; the shallow environmental application of constructing vertical groundwater permeable treatment walls (iron PRBs) and the much deeper application for petroleum recovery applications in existing hydrocarbon reservoirs. |
1998-1999 Major Breakthroughs Led to Current PRB Technologies and Processes |
|
Two major technology advances occurred during 1998 and early 1999;
1) the development of a rapid breaking enzyme capable of breaking even the highest pH iron gel mixtures, and
2) the development of the orientated metal frac initiation casing system allowing repeated multiple frac injections at various depth (stacked) horizons in order to form a continuous vertical wall. The new enzyme gel breaker assured the rapid (within 1-2 hours) and clean breakdown of all iron gel mixtures, even those with pH >10.
The new casing system enabled efficient PRB construction, by:
a) Enabled repeat injections at the same horizon.
b) Ensured inclusion coalescence between injection wells by casing delimiters and pore pressure relief, even with slight drilling offsets and/or casing orientation mis-alignment.
c) Enabled injection of high loadings of iron gel mixtures.
d) Resulted in greater productivity and efficiency, and simplifying PRB construction. |
2006-2008 Oil Field Casing System Developed and Deployed |
|
Mechanical expanded 4 wing split casing system deployed in Milk River tight gas reservoir in 2008. Two conventional wells were hydraulically fractured through perforations at seven (7) horizons. Two offset wells were stimulated using the split dilating casing systems at thge same seven (7) horizons. Hydraulic impedance tests on all of the stimulations determined the length and extent of the injected inclusions. The conventional stimulations did not produce fractures, in fact at the deeper horizons short bulbous cavity expansions were created in the formation, and at higher elevations, short horizontal fractures were developed, contrary to the prevailing stress field. The split casing stimulations produced long vertical inclusions at all depth horizons, clearly demonstrated for the first time at depth, that initiation is essential to propagate long vertical inclusions in ductile formations. |
2012 Second Generation Oil Field Casing System Developed and Deployed |
|
The second generation heavy oil casing system was deployed at tested in a shallow field trial. Thee installation
of multi-azimuth vertical propped planes from two (2) expanded split casing
sections in a sandy silt formation were performed. Each casing section contained six (6)
vertical propped planes at multiple azimuths that are coalesced by pore
pressure relief between the casing sections. Downhole expansion and splitting
of the 9-5/8” casing and cement quantified formation stiffness and strength, while
downhole photographs and packer impressions showed the split casing in the
locked open position. Each wing was stimulated independently of the other wings
with 12/20 proppant injected using a highly cross-linked gel through a
specialized treatment tool. Real time active resistivity monitoring quantified
the injected plane geometry from both sub-surface and surface resistivity
receivers. The field trials showed conclusively that multiple vertical
propped planes on various azimuths can be constructed from a single wellbore. The
field trials demonstrated the functionality of the expanded casing and
stimulated tools and showed that the vertical permeable propped planes could be
constructed on azimuth, with high in placed permeability. The geometry of the
injected planes was recorded in real-time by the active resistivity method. |
2013 Horizontal Well Open Hole Stimulation Tool Developed |
|
Horizontal open hole stimulation tool designed and developed for initiation and propagation of multiple vertical inclusion orthogonal to borehole axis and at multiple locations along the borehole.
A vertical well retrofit system was designed for existing vertical wells. The retrofit system is expected to be ready for deployment by end 2014. |
|
|
|